The Armstrong Project: UMC’s Agile, Flexible, Autonomous Manufacturing Facility
“We choose to go to the moon in this decade and do the other things, not because they are easy, but because they are hard, because that goal will serve to organize and measure the best of our energies and skills, because that challenge is one that we are willing to accept, one we are unwilling to postpone, and one which we intend to win, and the others, too.”
-John F Kennedy, September 12, 1962
You might say the same about UMC’s ongoing expansion, which we call The Armstrong Project. It’s a moonshot for manufacturing. UMC is committed to the journey because it will measure the best of our energies and skills—and is a challenge we are ready and willing to tackle and win.
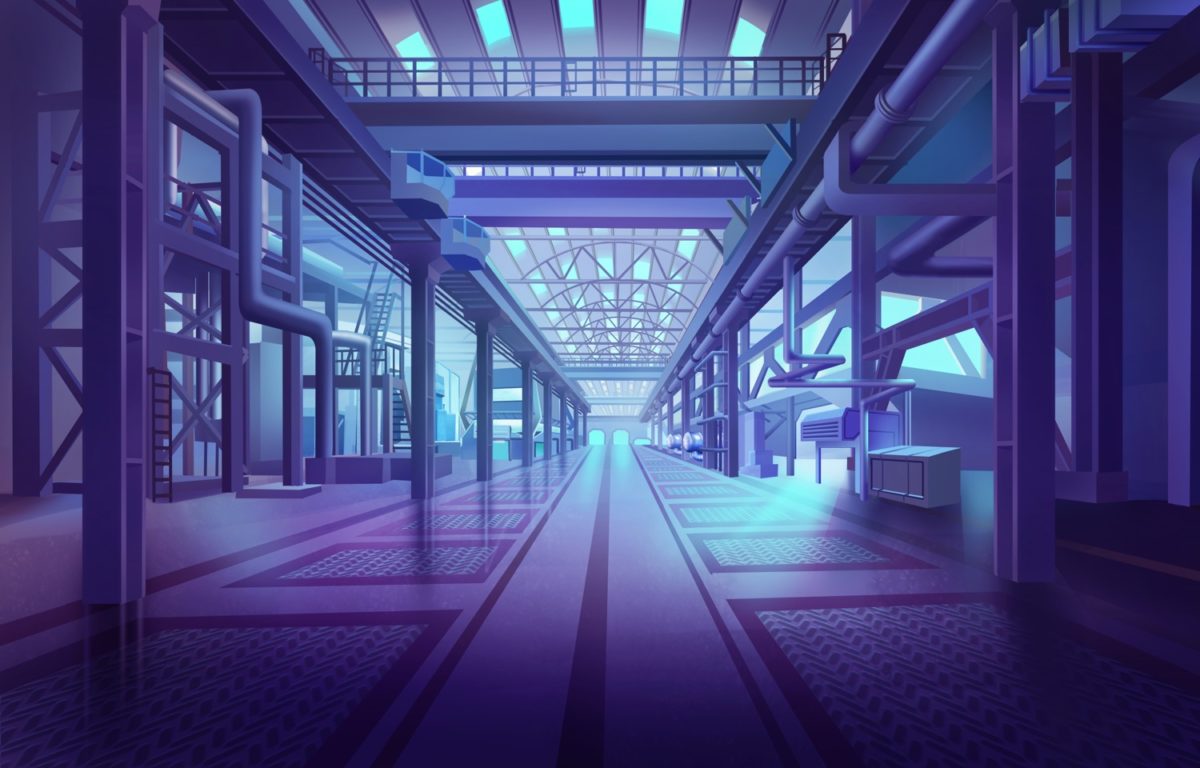
Issuing the Challenge in 2019
To get a sense of what we were up against, our CEO, Don Tomann, framed the challenge this way last year:
Draw a 40,000-square-foot box. Inside of that box, draw a 2,000-square-foot rectangle. In the rectangle, toss a piece of raw material on one end, and a cardboard box on the other end. Now challenge a team of engineers to fill this facility with a bunch of magic rectangles that can change the raw material into finished parts or products we can put in the box (and into the world). Huh? See—you might as well have asked us to put a man on the moon.
As the NASA story goes, the engineers were none too happy after the JFK speech. I suspect when the engineers heard Kennedy, they probably threw their hands up and said, “Well, you might as well have asked us to build an agile, flexible, autonomous manufacturing facility.”
Indirectly we have to thank NASA for the inspiration. What a novel idea: an agile, flexible, autonomous manufacturing facility.
- Agile to be able to reconfigure equipment lines and automation to adapt to customer demand.
- Flexible to service multiple product configurations, customers, and industry sectors.
- And to be autonomous: Layers of mechanical, logistical, ancillary, and information that will enable autonomous operations.
Defining the Design
Since the inception of our Armstrong Project, our CEO Don Tomann, our UMC team, and our architectural firm designed a visually stunning facility and cleared a path with the city to start construction with the city. To get the Armstrong project to groundbreaking, the Automation Engineering team—which includes Scott Peterson, Brian DeGrote, Jonathan Garcia, and Jessica Hanson—has been established and is leading the Armstrong project through the next phase, design review of the internal specifications.
The Automation Engineering team focused on marrying the UMC manufacturing vision to the facility’s internal specifications. They defined space for equipment lines, equipment transportation, automation lanes, maintenance support, training, process development, staffing amenities, and access. They also identified space and equipment to automate ancillary services such as air and water supply, bulk fluid storage and distribution, waste metal, and waste fluid recovery systems. The second pass at design input is now in the architect’s hands to finalize building design.
The Facility of Tomorrow
The moon landing JFK proposed in 1962 took our nation’s best and brightest seven years to accomplish. UMC’s goal of agile, flexible, autonomous manufacturing will not just be the building construction—a feat in itself!—but a long-term strategy to continue to maintain our role as a manufacturing leader.
Now that we finished the arduous work of defining our “box” as an agile, flexible, autonomous manufacturing facility, we can start talking about those “magic rectangles.”
Stay tuned!