Can Robots Help Inspect Precision Parts?
Tackling the Next Level of Advanced Automation in Precision Manufacturing
Innovation and automation go hand-in-hand in manufacturing and neither can be successful without a unified vision and a high level of teamwork. UMC has embraced automation to improve manufacturing and maximize the time and talents of our employees. Some processes are easier to automate than others, but we’re constantly pushing ourselves and our technology to achieve results that others might think impossible.
So, when our employees suggested we look at automating our coordinate measuring machine (CMM) process, we agreed to tackle the ambitious challenge as a team.

Exacting Inspection Required
In the highly regulated industries we serve, many parts require 100 percent inspection. Complete inspection means that we test every part to ensure its features meet the required specifications. We use a coordinated measuring machine, or CMM, to take and record measurements of the part. The CMM senses hundreds of discrete points on the surface of the part with a probe and records and verifies their coordinates against specified dimensions. This exacting work results in extremely precise measurements, down to 5/100000, or .00005 of an inch. For perspective, a human hair is, on average, .004 inches thick.
To start the process, the CMM operator must load the part into the machine with extreme accuracy, often using fixtures, or work holding support devices, to hold the part in place. Each part must be loaded individually with as little variance in placement as possible. It’s painstaking, repetitive work, often requiring 70-80 hours of continuous sitting. The operator loads the part, waits approximately five minutes for the inspection process to run, and then loads another part.
Delegating a Disliked Task
The idea of automating the loading of the CMM machines was embraced and brought to life by the people who were doing it manually every day. Mundane tasks, especially those that may pose risks or injury to employees, are the first jobs considered for automation.
Scott Peterson, senior quality engineer, notes, “Nobody enjoyed this part of the process. We have better uses for our people in the areas of decision making, problem-solving, and improving processes. We don’t need our skilled people facilitating data collection.”
Not only do people dislike this kind of work, but humans are also not the best fit for these tasks. If the person loading parts is called away or distracted for any reason, throughput—the number of parts passing through the inspection process—drops.
“Our throughput before automation was only about 25 percent of what we target with the automated process,” says Peterson.
That lower throughput is due to the high volume, fast-paced, repetitive nature of loading the parts over and over again. The person aligning the part often needs to use additional fixtures to load the part and remember to take that fixture off before running the inspection. Forgetting a step or getting called away in the middle of the process can cause errors and downtime.
Robots don’t require a secondary tool to line the part up. They don’t get bored or distracted, and they can be programmed to repeatedly complete precision alignment and precision measurement to the same standards every time, without the variation that comes into play with human interaction.
Finding the Right Robot
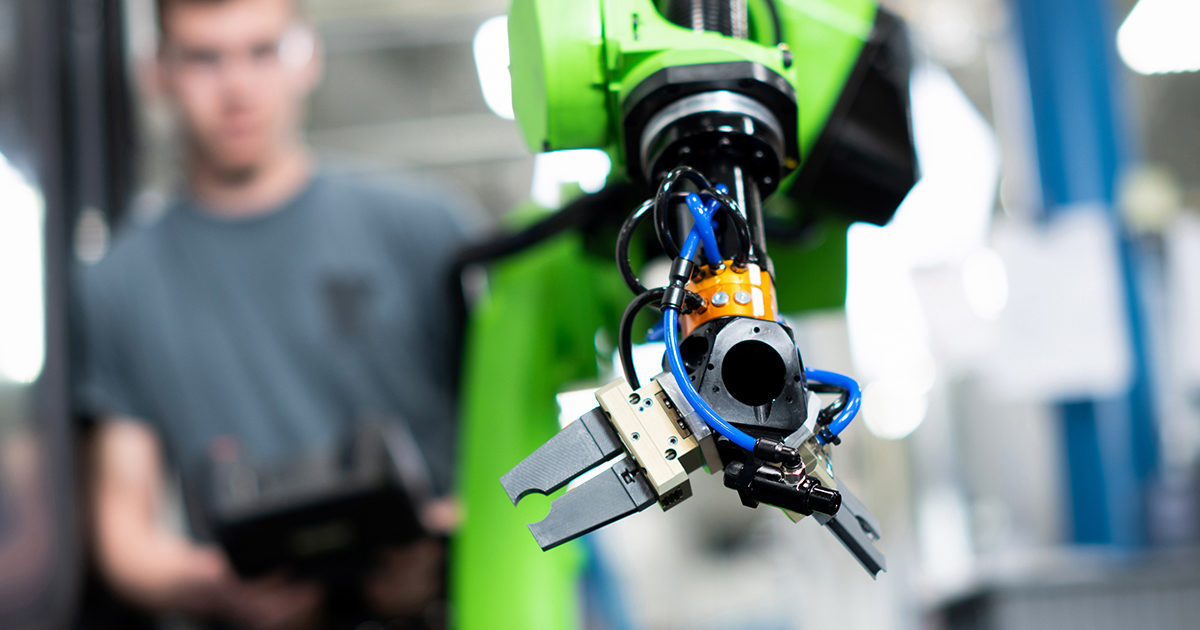
After targeting the CMM process for automation, we set out to find technology advanced and precise enough to hold the tight tolerances and safety standards required for the exacting inspection standards of UMC and our customers. We partnered with Productivity, Inc. to identify a robot that could reach four feet, carry up to 6 kilograms, and precisely place an object within two-thousandths of an inch.
After we found the technology we believed could do the job, we set out to push the robot to meet our exacting specifications. We looked at how efficient our process was before we brought in automation and debugged and improved our programs to be more reliable for the robot. We expanded our CMM lab to fit the new machine and developed some creative tooling to support the automation. It was a collaborative process involving more than 30 people, from designers and quality engineers to CMM programmers, a tool integration team, and the maintenance department
Measuring Our Success
Although we’ve done robotic integration projects before, this was the 1st CMM we automated. The precision required made this project one of the most complicated we’ve attempted. We were challenged and pushed outside of our comfort zone with the hope that the results would be worth the effort.
The robot immediately took on the dreaded task of 100% inspecting. Considering staffing shift gaps and need for our technicians to multi-task to support daily production demand, this effort normally required 6-8 days effort from our staff of 7 technicians working day/night and weekend shifts. The part lead time and CMM capacity consumption was disproportionate the actual inspection time.
The 100% inspection was completed uninterrupted without 0 missloads and 0 re-inspections in just over a day. Considering the annual demand of the part and the throughput improvement achieved this is equal to one-half an additional CMM. But, the moment of truth actually came a few days earlier when we completed our Gage Repeatability & Reproducibility (Gage R&R) study, a methodology used to define the amount of variation in the measurement data due to the measurement system.
The reproducibility, or amount of variation introduced by operator interaction, improved by 100 percent and reduced the overall Gage R&R percentage of tolerance used by 50 percent. These results show that the automation reduced operator variation in the process, allowing us to more clearly and quickly identify the variation coming from the inspection equipment—a huge win, making inspection more efficient and accurate.
Automating this process has also allowed people to learn new skills and freed up our employees to add more value to the dynamic and complex projects we’re working on for our customers.
“We will be challenging our staff to interact, learn and identify opportunities to apply automation, creating opportunity for our CMM programmers and technicians to develop new skills” says Peterson. “It’s a great opportunity to learn a new piece of equipment that will be there for a long time.”
What’s Next

We plan to continue to introduce automation into our CMM process as well as other areas where it will benefit our employees and customers. Every automation project brings new lessons, growth, and opportunity. There is always the risk that something won’t work, and the risk of failure increases as we push the boundaries of technology further and expand our creativity around what we can automate.
Together we’ve decided that, if we consider ourselves innovators in manufacturing, the calculated risk of moving forward far outweighs the risk of doing things the same way we’ve done them in the past.
Nobody enjoyed this part of the process. We have better uses for our people in the areas of decision making, problem-solving, and improving processes. We don’t need our skilled people facilitating data collection.
Scott Peterson, Senior Quality Engineer